Progettazione meccanica
La progettazione meccanica è il processo di creazione di soluzioni tecniche per risolvere problemi meccanici.[1][2]
Storia[modifica | modifica wikitesto]
La storia della progettazione meccanica è un percorso lungo e ricco che abbraccia molti secoli di progresso tecnologico e innovazione. Sin dai tempi antichi, gli esseri umani hanno cercato di creare dispositivi e macchine per semplificare il lavoro e migliorare la qualità della vita. Di seguito è riportata una panoramica generale della storia della progettazione meccanica.
Antichità[modifica | modifica wikitesto]
- Circa 4.000 a.C.: Nella Mesopotamia e nell'Antico Egitto, gli artigiani svilupparono tecniche per la lavorazione dei metalli, inclusa la produzione di utensili e armi.
- Circa 2.500 a.C.: Gli antichi egizi costruirono le prime leve, carrucole e sistemi di irrigazione che utilizzavano principi meccanici per semplificare le attività quotidiane.
Età classica[modifica | modifica wikitesto]
- IV secolo a.C.: Archimede, un ingegnere e matematico greco, sviluppò importanti principi meccanici, tra cui la leva, il paranco e la vite di Archimede.
- I secolo a.C.: Eroe di Alessandria, un ingegnere greco, descrisse il principio delle macchine a vapore, che avrebbe aperto la strada alla futura rivoluzione industriale.
Medioevo[modifica | modifica wikitesto]
- IX-X secolo: Durante il periodo dell'Alto Medioevo, gli ingegneri musulmani come Al-Jazari fecero importanti contributi all'ingegneria meccanica, descrivendo e costruendo dispositivi come orologi ad acqua, automi e sistemi idraulici complessi.
- XIII secolo: L'ingegnere italiano Villard de Honnecourt compilò un famoso manoscritto contenente disegni e descrizioni di macchine e dispositivi meccanici.
Rinascimento[modifica | modifica wikitesto]
- XV secolo: Con l'avvento della stampa e la diffusione dei libri, le conoscenze e le idee sulla progettazione meccanica furono più accessibili. L'invenzione della stampa a caratteri mobili da parte di Johannes Gutenberg nel 1450 segnò un punto di svolta nella diffusione delle conoscenze tecniche.
Età moderna[modifica | modifica wikitesto]
- XVIII secolo: Durante la Rivoluzione Industriale, la progettazione meccanica fece progressi significativi. James Watt sviluppò e perfezionò il motore a vapore, rendendo possibile la sua applicazione industriale su larga scala.
- XIX secolo: L'invenzione e l'evoluzione della macchina a vapore, la produzione meccanizzata e la diffusione delle ferrovie portarono a un rapido sviluppo della progettazione meccanica. Pionieri come Eli Whitney, Henry Maudslay e Richard Roberts fecero importanti progressi nel campo delle macchine utensili e dell'ingegneria di precisione.
Età contemporanea[modifica | modifica wikitesto]
- XX secolo: L'avvento dell'elettronica, dell'automazione e dell'informatica ha rivoluzionato la progettazione meccanica. La computerizzazione e l'introduzione del design assistito da computer (CAD) hanno reso più efficiente la progettazione e la modellazione di parti e sistemi complessi.
- XXI secolo: La progettazione meccanica ha continuato a evolversi con l'introduzione di tecnologie avanzate come la stampa 3D, la robotica avanzata e l'intelligenza artificiale, consentendo la creazione di dispositivi e sistemi ancora più sofisticati.
La storia della progettazione meccanica è un continuum di innovazione e scoperta, in cui gli ingegneri e gli inventori hanno lavorato per risolvere problemi e migliorare il modo in cui il mondo funziona. Continua a evolversi con il passare del tempo e continua a guidare il progresso tecnologico in tutti gli ambiti della vita quotidiana.
Aspetti della progettazione meccanica[modifica | modifica wikitesto]
La progettazione meccanica comprende diversi aspetti, variabili a seconda delle necessità e richieste progettuali, quali:[1][2]
- lo studio di parti singole o di sistemi meccanici complessi
- dimensionamento dei componenti
- la modellazione e la simulazione del comportamento meccanico dei componenti.
- Creazione di un prototipo reale
- la scelta dei materiali
- Identificazione dei processi di fabbricazione e selezione delle macchine utensili
- l'analisi del carico e della resistenza dei materiali
- la modellazione e la simulazione del comportamento meccanico dei componenti.
- preparazione di un disegno tecnico contenente tutte le informazioni precedenti
Studio di parti e sistemi meccanici complessi[modifica | modifica wikitesto]
Studiare un componente in meccanica richiede un approccio sistematico e analitico. Di seguito alcuni aspetti da tenere in considerazione:
- Analisi del componente: studiare attentamente la sua geometria, le dimensioni, le caratteristiche costruttive e le connessioni con altri elementi o sistemi. Comprendere la sua funzione nel contesto più ampio dell'applicazione.
- Identificazione dei requisiti: Definire chiaramente i requisiti del componente. Questi possono includere specifiche di resistenza, rigidità, durata, precisione, tolleranze, requisiti di assemblaggio e altri parametri pertinenti. Considerare anche eventuali requisiti normativi o standard di settore.
- Collegamenti e interfacce: Analizzare come il componente si collega ad altri elementi o sistemi. Valutare i tipi di giunzione, come ad esempio saldature, viti, adesivi o incastri. È importante comprendere i requisiti di resistenza, tenuta e precisione delle interfacce per garantire che il componente funzioni correttamente nel suo contesto.
- Funzione e scopo: Comprendere la funzione del componente all'interno dell'intero sistema o dell'applicazione in cui viene utilizzato. Identificare quali compiti specifici deve svolgere, quali carichi deve sopportare e quali vincoli operativi deve affrontare. Questo aiuta a definire le specifiche e i requisiti che il componente deve soddisfare.
- Stato di servizio: Valutare le condizioni operative in cui il componente dovrà operare. Considerare fattori come temperature, umidità, vibrazioni, carichi ciclici, corrosione o altri ambienti aggressivi. Queste informazioni influenzeranno la scelta dei materiali, i trattamenti superficiali e le considerazioni di durata del componente.
L'analisi approfondita del componente consente di ottenere una comprensione dettagliata delle sue caratteristiche, delle sue limitazioni e delle sue esigenze specifiche. Questo è il punto di partenza per condurre ulteriori analisi e valutazioni per garantire che il componente soddisfi le specifiche richieste e si comporti in modo affidabile nel suo contesto di utilizzo.
Dimensionamento[modifica | modifica wikitesto]

Il dimensionamento è il processo di determinazione delle dimensioni appropriate e delle caratteristiche geometriche di un componente o di un sistema meccanico al fine di garantire la sua funzionalità e la sua sicurezza durante l'uso.[3]
Per un corretto dimensionamento, è necessario tenere in considerazione, oltre alle dimensioni "ideali" del pezzo da costruire, anche le possibili tolleranze associate a tali dimensioni. Le tolleranze sono specifiche dimensionali che vengono definite per garantire che i componenti meccanici funzionino correttamente e si adattino perfettamente ad altri componenti con cui devono interagire. In altre parole, le tolleranze sono la differenza tra la dimensione nominale di un componente e le dimensioni massime e minime accettabili per quella specifica dimensione.[3] A seconda delle finalità, vengono definite tolleranze dimensionali o tolleranze geometriche.[3]
Modellazione 3D[modifica | modifica wikitesto]

La modellazione 3D è una tecnica di progettazione che consente di creare modelli tridimensionali di componenti o sistemi meccanici utilizzando software di modellazione 3D. In questo processo, il progettista utilizza un software di modellazione 3D per creare un modello virtuale del componente o del sistema meccanico. Il software permette di creare forme e geometrie complesse, aggiungere dettagli e specificare materiali e proprietà fisiche.[3]
La modellazione 3D in meccanica offre numerosi vantaggi rispetto ai metodi di progettazione tradizionali, come il disegno manuale o la modellazione 2D. Ad esempio, la modellazione 3D consente di visualizzare il componente o il sistema meccanico da diverse angolazioni, di analizzare le interazioni tra le parti, di valutare le sollecitazioni e le deformazioni e di simulare il comportamento in situazioni di carico e di stress. Inoltre, permette di creare prototipi virtuali, che possono essere utilizzati per effettuare test e analisi senza la necessità di produrre fisicamente il componente. Questo consente di risparmiare tempo e denaro durante la fase di sviluppo del progetto, nonché di identificare potenziali problemi o miglioramenti prima di produrre il componente fisicamente.[3]
Modellazione inversa[modifica | modifica wikitesto]
Un particolare tipo di modellazione è la modellazione inversa, il cui scopo è quello di replicare un modello 3D di un pezzo fisico esistente, di cui non si ha il modello CAD originale o il disegno tecnico nativo. La modellazione può essere eseguita con strumenti di misura quali ad esempio calibro, micrometro e comparatore, oppure con moderni strumenti come scanner 3D o tastatori 3D.
Creazione di prototipi[modifica | modifica wikitesto]
La creazione di prototipi svolge un ruolo fondamentale nel processo di progettazione meccanica. Consiste nella creazione di modelli fisici o virtuali iniziali delle parti o dei sistemi che si desidera realizzare, al fine di testare e valutare le soluzioni proposte prima di passare alla produzione finale.
Ecco alcuni punti chiave riguardanti la progettazione di prototipi nella progettazione meccanica:
- Verifica concettuale: La progettazione di un prototipo consente di testare e verificare la fattibilità del concetto progettuale. Attraverso il prototipo, è possibile valutare le funzionalità, le prestazioni e le interazioni dei componenti meccanici in un ambiente controllato.
- Identificazione e risoluzione dei problemi: Il prototipo aiuta a identificare eventuali difetti di progettazione, limitazioni o problemi di funzionamento che potrebbero non essere stati previsti durante la fase di progettazione iniziale. Questo consente di apportare modifiche, apportare miglioramenti e risolvere i problemi prima di avanzare nella produzione di massa.
- Ottimizzazione del design: La progettazione di prototipi consente di valutare diverse soluzioni di design, testarle e confrontarle direttamente. Attraverso iterazioni successive, è possibile ottimizzare il design, migliorando aspetti come la resistenza strutturale, l'efficienza, l'ergonomia o altre specifiche di progetto.
- Test di funzionalità e performance: I prototipi consentono di eseguire test di funzionalità e di valutare le performance del sistema in condizioni realistiche. Questo può includere test di stress, test di durata, simulazioni di carico e prove funzionali per garantire che il prodotto finale soddisfi i requisiti desiderati.
- Comunicazione e feedback: I prototipi fisici o virtuali possono essere presentati agli stakeholder, ai clienti o agli utenti finali per ottenere feedback e commenti preziosi. Questo aiuta a raccogliere informazioni sulla soddisfazione dei requisiti, sulle preferenze degli utenti o su possibili miglioramenti, consentendo un'iterazione del design più mirata.
- Riduzione dei rischi: La progettazione di prototipi consente di individuare e mitigare i rischi tecnici, finanziari o di produzione associati al prodotto finale. Identificare e affrontare i problemi in una fase precoce riduce i costi e i tempi di sviluppo, migliorando l'affidabilità e la qualità del prodotto finale.
Oggi, la progettazione di prototipi può avvenire utilizzando diverse metodologie, come la prototipazione rapida con la stampa 3D, l'utilizzo di software di simulazione e modellazione avanzata o la creazione di prototipi virtuali attraverso la modellazione CAD. Queste tecnologie consentono di ridurre i tempi di sviluppo e i costi associati alla creazione di prototipi fisici, consentendo iterazioni più rapide e un processo di progettazione più efficiente.
Scelta dei materiali[modifica | modifica wikitesto]
I materiali più comunemente utilizzati nella progettazione meccanica,[4] a seconda delle esigenze di progettazione e di utilizzo, sono:
- Materiali metallici: metalli e loro leghe
- Acciaio: utilizzato per la sua resistenza e durezza, l'acciaio è uno dei materiali più utilizzati nella lavorazione meccanica.[4]
- Ghisa: la ghisa è un materiale duro e resistente, spesso utilizzato nella produzione di parti di macchine per applicazioni pesanti.[4]
- Alluminio: leggero, resistente alla corrosione e facile da lavorare, l'alluminio è ampiamente utilizzato in applicazioni aeronautiche, automobilistiche ed elettroniche.[4]
- Rame: noto per la sua alta conducibilità elettrica e termica, il rame è spesso utilizzato per componenti elettronici e per l'industria automobilistica.[4]
- Leghe di titanio: resistente alla corrosione, leggero e ad alta resistenza, il titanio viene spesso utilizzato in applicazioni aeronautiche, mediche e di difesa.[4]
- Bronzo: noto per la sua durezza e resistenza alla corrosione, il bronzo è spesso utilizzato per componenti marini, automobilistici ed elettrici.[4]
- Materie plastiche: leggere, resistenti e versatili, le materie plastiche sono spesso utilizzate nella produzione di parti e componenti di macchine.[4]
- Materiali compositi: composti da una combinazione di materiali diversi, come fibre di vetro o carbonio e resina, i materiali compositi sono noti per la loro leggerezza e resistenza ed sono spesso utilizzati nell'industria aerospaziale e nel motorsport.[4]
La scelta del materiale più idoneo per una particolare applicazione deve tenere conto anche delle modifiche (chimiche, strutturali, superficiali, ecc.) a cui i materiali possono essere sottoposti per migliorarne le caratteristiche. Esempi di tali modifiche sono:
- trattamenti termici
- finitura superficiale (ad esempio: levigatura, lappatura, lucidatura, godronatura, ecc.)
- vulcanizzazione della gomma
- aggiunta di additivi
I trattamenti termici sono operazioni che hanno lo scopo di migliorare le proprietà meccaniche dei materiali grezzi. A seconda delle caratteristiche meccaniche richieste dal progetto, si possono applicare uno o più trattamenti termici consecutivi ad un componente meccanico, che vanno a modificare proprietà quali la resistenza, la durezza, la tenacità fino alla la microstruttura interna del materiale.
Trattamenti termici dell'acciaio[modifica | modifica wikitesto]
I trattamenti termici sono utilizzati per migliorare le proprietà meccaniche dei materiali, in particolare degli acciai. I trattamenti termici possono aumentare la durezza, la resistenza, la tenacità, la resistenza all'usura e la resistenza alla corrosione dell'acciaio. In generale, i trattamenti termici mirano a modificare la microstruttura dell'acciaio, ovvero la disposizione degli atomi all'interno del materiale. Riscaldando l'acciaio a temperature elevate e poi raffreddandolo in modo controllato, si possono ottenere differenti microstrutture e, di conseguenza, differenti proprietà meccaniche.[4]
I trattamenti termici possono essere utilizzati per produrre materiali ad alta resistenza, come le leghe d'alluminio ad alta resistenza utilizzate nell'industria aerospaziale, o per migliorare la lavorabilità degli acciai, come la bonifica utilizzata per ottenere un acciaio tenace e facilmente lavorabile.[4]
Gli acciai ideali per questo tipo di trattamento termico si definiscono acciai da bonifica. I possibili trattamenti:[4]
- Rinvenimento: processo di riscaldamento dell'acciaio ad alta temperatura seguito da un raffreddamento graduale. Questo trattamento riduce la durezza e la fragilità dell'acciaio, aumentando al contempo la sua tenacità e resistenza.[4]
- Ricottura: processo di riscaldamento dell'acciaio ad alta temperatura seguito da un raffreddamento lento per ridurre la durezza e migliorare la lavorabilità dell'acciaio.[4]
- Normalizzazione: processo di riscaldamento dell'acciaio a temperature elevate seguito da un raffreddamento in aria. Questo trattamento migliora la microstruttura dell'acciaio, aumentandone la durezza e la resistenza.[4]
- Tempra: processo di riscaldamento dell'acciaio a temperature elevate seguito da un rapido raffreddamento in acqua o in olio. Questo trattamento aumenta la durezza dell'acciaio, ma può anche rendere l'acciaio fragile.[4]
- Cementazione: processo di riscaldamento dell'acciaio a temperature elevate in presenza di gas carburante per creare uno strato esterno di acciaio con un alto contenuto di carbonio. Questo strato più duro e resistente viene chiamato "strato cementato".[4]
- Nitrocarburazione: processo di riscaldamento dell'acciaio in presenza di gas contenenti azoto e carbonio per creare uno strato superficiale duro e resistente con alta resistenza all'usura.[4]
- Indurimento superficiale (Surface Hardening) - processo di riscaldamento dell'acciaio a temperature elevate, seguito da un raffreddamento rapido solo sulla superficie dell'acciaio, creando uno strato superficiale duro e resistente.[4]
Trattamenti termici della ghisa[modifica | modifica wikitesto]
I trattamenti termici della ghisa sono meno comuni rispetto a quelli dell'acciaio, ma possono essere utili per migliorare le proprietà meccaniche di specifici tipi di ghisa, in base all'applicazione finale.[4]
- Normalizzazione: Consiste nel riscaldamento della ghisa a una temperatura superiore alla sua temperatura di transizione austenitica e successivo raffreddamento all'aria. Questo processo produce una struttura omogenea e fine, migliorando la tenacità e la resistenza all'usura del materiale.[4]
- Tempra: Consiste nel riscaldare la ghisa a una temperatura superiore alla sua temperatura di transizione austenitica, mantenere questa temperatura per un tempo sufficiente per ottenere la trasformazione dell'intera massa in austenite e successivamente raffreddare rapidamente la ghisa in acqua o in olio. Questo processo aumenta la durezza e la resistenza della ghisa, ma la rende anche fragile e meno tenace.[4]
- Rinvenitura: Consiste nel riscaldare la ghisa temprata a una temperatura inferiore rispetto alla tempra e mantenere questa temperatura per un periodo di tempo sufficiente a ridurre la fragilità. Questo trattamento termico riduce la durezza della ghisa e aumenta la sua tenacità. La rinvenitura viene utilizzata dopo la tempra per aumentare la tenacità della ghisa.[4]
Selezione delle macchine utensili[modifica | modifica wikitesto]
Le macchine della lavorazione meccanica sono strumenti utilizzati per tagliare, forare, plasmare e formare il materiale grezzo in parti e componenti meccanici di precisione. Queste macchine, spesso utilizzate in ambienti industriali e manifatturieri, sfruttano la forza e la precisione meccanica per creare parti di alta precisione.[5]
Macchina | Descrizione | Immagine |
---|---|---|
Tornio | Una macchina che ruota il pezzo di lavoro su un mandrino mentre uno o più strumenti da taglio tagliano il materiale in modo simmetrico per creare parti cilindriche, coniche e filettate. | ![]() |
Fresatrice | una macchina che utilizza strumenti rotanti con taglienti multipli per rimuovere il materiale dal pezzo di lavoro e creare forme complesse. | |
Pressa | una macchina che utilizza una forza compressiva per plasmare, tagliare o formare il materiale. | |
Macchina per la saldatura | una macchina che utilizza il calore e la pressione per unire due o più pezzi di materiale. | |
Macchina per la foratura: | una macchina che utilizza una punta di trapano per perforare un pezzo di lavoro. | |
Macchina per il taglio laser | una macchina che utilizza un raggio laser per tagliare il materiale in modo preciso e dettagliato. | |
Macchina per il taglio ad acqua | una macchina che utilizza un getto d'acqua ad alta pressione per tagliare il materiale. | |
Macchina per la piegatura | una macchina che utilizza la pressione per piegare il materiale in forme desiderate. | |
Alesatrice | una macchina che utilizza una fresa per tagliare con precisione fori cilindrici in un pezzo di lavoro. L'alesatrice è utilizzata per creare fori di dimensioni precise e può anche essere utilizzata per creare fori coniche o profilati. | |
Dentatrice | una macchina che utilizza una serie di taglienti per creare denti su ingranaggi, pulegge e altri componenti meccanici. La dentatrice è utilizzata per creare dentature precise e uniformi su pezzi di lavoro. | ![]() |
Piallatrice | una macchina che utilizza una lama di taglio per rimuovere il materiale in eccesso dalle superfici piane di un pezzo di lavoro. La piallatrice è utilizzata per creare superfici lisce e uniformi su pezzi di lavoro. | |
Macchina a controllo numerico (CNC) | una macchina che utilizza un computer per controllare la produzione di parti. Le macchine CNC possono essere utilizzate per la lavorazione di materiali come il metallo, la plastica e il legno, e sono in grado di eseguire una varietà di operazioni di taglio, foratura e fresatura con precisione e ripetibilità. | ![]() |
Limatrice | una macchina impiegata per sgrossare o scanalare la superficie piana di un pezzo. | ![]() |
Stozzatrice o mortasatrice | una macchina simile alla limatrice, ma la slitta portautensile lavora con moto rettilineo alternato verticale invece che orizzontale, e con corsa più breve. La slitta può anche essere inclinata. | ![]() |
Analisi dei carichi e della resistenza dei materiali[modifica | modifica wikitesto]
L'analisi dei carichi e della resistenza dei materiali in meccanica servono per valutare la capacità di un componente o di una struttura di sopportare sollecitazioni e carichi senza subire danni o cedimenti. Ecco alcune informazioni chiave su questo argomento:
Analisi dei carichi:
- Tipi di carico: I carichi possono essere di diversi tipi, come carichi statici (costanti nel tempo), carichi dinamici (variano nel tempo), carichi termici, carichi di torsione, carichi di compressione, carichi di trazione, carichi di flessione, carichi di taglio e molti altri. È importante identificare correttamente i tipi di carico che agiscono sul componente per valutare adeguatamente le sollecitazioni che si generano.
- Sollecitazioni e deformazioni: I carichi applicati a un componente generano sollecitazioni interne che determinano lo stato di tensione e deformazione all'interno del materiale. L'analisi delle sollecitazioni comprende la determinazione degli sforzi (tensioni) e delle deformazioni in punti critici del componente.
- Fattori di sicurezza: Per garantire la durata e l'affidabilità del componente, viene spesso utilizzato un fattore di sicurezza. Il fattore di sicurezza rappresenta il rapporto tra la resistenza del materiale e il carico massimo previsto. Assicurando che il fattore di sicurezza sia adeguato, si riduce il rischio di cedimenti o deformazioni permanenti.
Resistenza dei materiali:
- Proprietà dei materiali: I materiali hanno diverse proprietà meccaniche, come resistenza alla trazione, resistenza alla compressione, resistenza al taglio, durezza, resilienza e duttilità. Queste proprietà influenzano la capacità del materiale di sopportare carichi e sollecitazioni senza subire cedimenti o deformazioni permanenti.
- Diagramma sforzo-deformazione: Il diagramma sforzo-deformazione rappresenta la risposta meccanica di un materiale quando viene sottoposto a carichi crescenti. Questo diagramma fornisce informazioni sul comportamento elastico, plastico e di rottura del materiale.
- Tensione ammissibile: La tensione ammissibile è il valore massimo di sforzo che il materiale può sostenere senza superare la sua resistenza. La tensione ammissibile dipende dal tipo di materiale, dalla sua resistenza e da altri fattori, ed è spesso determinata attraverso test di laboratorio e standard di settore.
- Affaticamento: L'affaticamento è un fenomeno che si verifica quando un componente è sottoposto a carichi ciclici ripetitivi nel tempo. Può portare a cedimenti anche se i carichi applicati sono inferiori alla tensione ammissibile. L'analisi di resistenza alla fatica è quindi importante per garantire la durata del componente.
L'analisi dei carichi e della resistenza dei materiali permette di valutare la capacità di un componente di sopportare carichi previsti e di prevenire cedimenti o deformazioni indesiderate. È fondamentale considerare attentamente questi aspetti durante la progettazione e la valutazione di componenti meccanici per garantire la loro affidabilità e sicurezza.
Disegno tecnico[modifica | modifica wikitesto]

Il disegno tecnico è la rappresentazione grafica di un componente o di un sistema meccanico, realizzato in conformità alle norme e alle convenzioni dell'industria meccanica. Questo tipo di disegno viene utilizzato per descrivere in dettaglio le caratteristiche fisiche, geometriche e funzionali del componente o del sistema, nonché per indicare le specifiche di produzione. La rappresentazione grafica comprende solitamente una vista frontale, una vista laterale e una vista superiore del componente o del sistema, insieme ad altre viste o proiezioni necessarie per descrivere tutte le caratteristiche importanti.[3]
Il disegno tecnico completa la fase di progettazione di un progetto meccanico: in esso sono contenute tutte le informazioni necessarie per la fase esecutiva successiva.
Componenti meccanici[modifica | modifica wikitesto]
Eseguita la produzione dei singoli componenti, segue la fase di assemblaggio, ovvero l'interazione tra due o più componenti, individuata in una macchina semplice o la combinazione di esse, ovvero macchina complessa. I componenti a disposizione del progettista meccanico per unire due o più componenti insieme in modo sicuro e stabile seguendo tali principi sono numerose.[6]
Organi di collegamento filettati[modifica | modifica wikitesto]
Gli organi di collegamento filettati, come viti, bulloni e dadi, ovvero organi dotati di filettatura, sono tra i più comuni e versatili utilizzati in meccanica. La scelta del giusto organo di collegamento filettato dipende dalle esigenze specifiche dell'applicazione, come ad esempio la forza richiesta, il materiale da fissare e le condizioni ambientali.[6]
Organo | Descrizione | Immagine |
---|---|---|
Vite (meccanica) | organi di collegamento costituiti da un gambo filettato e una testa che può essere a cupola, cilindrica, svasata, tonda o a croce. | ![]() |
Vite prigioniera | un particolare tipo di vite che si presenta senza testa e filettata in ambedue le estremità, fatta per essere avvitata su una madrevite. | |
Bullone | organi di collegamento costituiti da un gambo filettato e una testa esagonale o a cupola per facilitare la serratura con una chiave. | ![]() |
Dado (meccanica) | organi di collegamento costituiti da un pezzo di forma poligonale, solitamente esagonale, con un foro filettato al centro. | ![]() |
Organi di collegamento non filettati[modifica | modifica wikitesto]
Gli organi di collegamento non filettati sono metodi di unione tra componenti meccanici privi di un sistema di filettatura che consentono comunque di separare le parti in seguito, facilitando l'assemblaggio, la manutenzione o la sostituzione dei componenti. Questi collegamenti sono progettati per essere rimovibili senza danneggiare in modo permanente le parti coinvolte.[6]
Organo | Descrizione | Immagine |
---|---|---|
Spina (meccanica) | organi di collegamento utilizzati per il fissaggio di parti cilindriche, come alberi e fori, mediante l'interposizione di una parte cilindrica che si adatta perfettamente al foro. | ![]() |
Chiavetta (meccanica) | organi di collegamento utilizzati per il fissaggio di parti cilindriche, come alberi e pulegge, mediante l'interposizione di una lamina di metallo o di plastica che si adatta alla forma del foro. | ![]() |
Linguetta (meccanica) | organi di collegamento utilizzati per il fissaggio di parti cilindriche, come alberi e pulegge, mediante l'interposizione di una lamina di metallo o di plastica che si adatta alla forma del foro. | ![]() |
Rondella (meccanica) | organi di collegamento utilizzati per il fissaggio di parti cilindriche mediante l'interposizione di un anello di metallo o di plastica che si adatta alla forma del foro. | ![]() |
Calettatore | organi di collegamento utilizzati per il fissaggio di parti cilindriche, come alberi e pulegge, mediante l'interposizione di una lamina di metallo o di plastica che si adatta alla forma del foro. | |
Bronzina | una bronzina è un elemento meccanico utilizzato per supportare un'altra parte in movimento, ad esempio un albero rotante, e a ridurre l'attrito tra le parti. Le bronzine sono generalmente realizzate in leghe metalliche, come il bronzo, l'ottone o l'acciaio, e possono essere di diversi tipi, come bronzine a boccole, a coppa, a piattello, etc. | |
Boccola | una boccola è un elemento meccanico utilizzato per adattare la dimensione di un foro a quella di un albero o di una vite. Le boccole sono generalmente realizzate in metallo o in plastica e possono essere di diversi tipi, come boccole cilindriche, coniche, a flangia, a denti, etc. | |
un anello d'arresto, noto anche come anello di sicurezza, è un componente utilizzato per prevenire lo spostamento o lo scivolamento di una parte su un albero o un perno. L'anello d'arresto viene inserito all'interno di una scanalatura o di un'apposita sede nell'albero o nel perno e viene utilizzato per trattenere o bloccare la parte in posizione.
Un particolare tipo di anello d'arresto detto Seegerring o anello Seeger. In funzione della loro posizione di lavoro vengono definiti anelli per albero o anelli per foro. |
![]() | |
Copiglia | La copiglia (o coppiglia) è un organo meccanico di unione, che impedisce ad un dado di svitarsi o ad un perno di sfilarsi dalla sua sede. | ![]() |
Collegamenti fissi[modifica | modifica wikitesto]
I collegamenti fissi sono metodi di unione tra componenti meccanici che creano una connessione permanente e non rimovibile. A differenza dei collegamenti smontabili, come viti e bulloni, i collegamenti fissi sono progettati per fornire una connessione stabile e resistente che non richiede di essere separata in seguito.[6]
Rivetto | utilizzato per realizzare dei collegamenti permanenti tra componenti di una struttura | ![]() |
Saldatura[modifica | modifica wikitesto]
Una particolate tipologia di collegamento fisso è la saldatura, un processo di unione permanente di due o più parti metalliche mediante fusione. È un metodo ampiamente utilizzato per creare collegamenti solidi, resistenti e duraturi tra le parti, consentendo di creare strutture complesse e robuste. Il processo di saldatura coinvolge l'applicazione di calore alle parti da unire, che provoca la fusione del metallo nelle zone interessate. Spesso viene utilizzato anche un materiale di riempimento fuso chiamato materiale di apporto, che si aggiunge al giunto per assicurare una connessione solida. La scelta della tecnica di saldatura dipende dai materiali coinvolti, dalle dimensioni e dalla geometria delle parti, dalle richieste di resistenza e durata, nonché dalle considerazioni economiche.
Innesti[modifica | modifica wikitesto]
Gli innesti sono dispositivi utilizzati per collegare o disconnettere due estremità d'albero coassiali. Gli innesti consentono di trasferire il movimento o la potenza tra le parti o di separarle rapidamente per scopi di manutenzione o sostituzione.
Alberi ed assi[modifica | modifica wikitesto]
Un albero è una componente meccanica lunga e rigida, generalmente cilindrica, che viene utilizzata per trasmettere il movimento rotatorio o la potenza tra diverse parti di una macchina o di un sistema meccanico. Quando la loro funzione è limitata a mantenere la posizione di un componente senza trasmettere momento torcente vengono detti assi. Sono caratterizzati da una lunghezza maggiore rispetto al loro diametro e sono progettati per resistere agli sforzi meccanici, come torsione, flessione, compressione e trazione, che si verificano durante il funzionamento.
Gli alberi vengono solitamente supportati da cuscinetti o boccole al fine di ridurre l'attrito e sostenere il carico durante la rotazione. Possono anche essere soggetti a trattamenti termici o rivestimenti superficiali per aumentarne la resistenza e la durata. Gli alberi sono progettati tenendo conto di fattori come il carico, la velocità, la durata, la rigidità e la facilità di montaggio e smontaggio. La progettazione di un albero richiede la considerazione di fattori come la resistenza dei materiali, la distribuzione dei carichi, la lubrificazione, la modalità di fissaggio e gli accoppiamenti con altre componenti del sistema meccanico.
Cuscinetti[modifica | modifica wikitesto]

i cuscinetti sono dispositivi utilizzati per ridurre l'attrito e fornire supporto rotazionale tra due superfici in movimento relativo. Essi consentono il movimento fluido e la riduzione dell'usura nelle applicazioni in cui si verificano rotazioni o movimenti lineari. Sono progettati per sostenere carichi, ridurre l'attrito e dissipare il calore generato dal movimento. Se non esistono blocchi meccanici essi vengono fissati su un albero tramite Anello d'arresto.
Guarnizioni[modifica | modifica wikitesto]
Le guarnizioni sono componenti utilizzati per sigillare lo spazio tra due superfici, creando una barriera che impedisce la fuoriuscita o l'ingresso di fluidi, gas o particelle solide. Le guarnizioni sono realizzate in materiali elastomerici, come gomma, silicone, poliuretano o materiali sintetici rinforzati. Possono assumere diverse forme e configurazioni a seconda delle esigenze specifiche dell'applicazione:
- Guarnizioni piane
- Guarnizioni a labbro
- Guarnizioni ad O-ring
- Guarnizioni a labirinto
Le guarnizioni sono selezionate in base alle caratteristiche dell'applicazione, come la temperatura, la pressione, il tipo di fluido o gas, e il tipo di movimento relativo tra le superfici. La corretta installazione e manutenzione delle guarnizioni sono importanti per garantire una tenuta affidabile e prevenire perdite o malfunzionamenti del sistema meccanico.
Molle[modifica | modifica wikitesto]

una molla è un elemento meccanico flessibile che viene utilizzato per immagazzinare energia potenziale elastica. Le molle sono progettate per deformarsi quando vengono applicate forze esterne e ritornare alla loro forma originale una volta che la forza viene rimossa.
Generazione del moto[modifica | modifica wikitesto]
Un attuatore è un dispositivo utilizzato per convertire l'energia in ingresso in un movimento o una forza di uscita. Gli attuatori sono componenti essenziali nei sistemi meccanici e vengono impiegati per generare o controllare il movimento di parti o componenti all'interno di una macchina o di un sistema. Gli attuatori possono essere di diversi tipi e utilizzano varie forme di energia, come energia elettrica, pneumatica, idraulica o meccanica, per generare il movimento desiderato. Ad esempio, un attuatore pneumatico utilizza l'energia dell'aria compressa per generare un movimento lineare o rotativo, mentre un attuatore elettrico utilizza l'energia elettrica per generare il movimento. Gli attuatori possono essere semplici o complessi, a seconda delle esigenze del sistema. Possono essere azionati manualmente, automaticamente o da un sistema di controllo, come un computer o un PLC (Programmable Logic Controller).
Attuatori meccanici[modifica | modifica wikitesto]
Gli attuatori meccanici sono dispositivi che utilizzano componenti meccanici, come leve, camme, ruote dentate o sistemi a cavi, per generare un movimento desiderato. Questi attuatori sono generalmente azionati manualmente o da altre sorgenti di energia, come un motore o un'altra macchina. Un esempio comune di attuatore meccanico è il sistema di sterzo in un veicolo, che utilizza una leva o un sistema a cremagliera e pignone per tradurre il movimento del volante in un movimento di rotazione delle ruote.
Giunti di trasmissione[modifica | modifica wikitesto]
I giunti di trasmissione sono dispositivi utilizzati per collegare alberi o assi rotanti al fine di trasmettere il movimento o la potenza tra di essi. Questi giunti consentono di compensare eventuali disallineamenti, fornire flessibilità e assorbire gli shock e le vibrazioni durante la trasmissione di potenza.
Ruote dentate[modifica | modifica wikitesto]
Una ruota dentata è un componente meccanico utilizzato per trasmettere il movimento e la potenza tra due alberi o assi rotanti. Consiste in una ruota circolare con denti disposti lungo il suo perimetro. I denti sono progettati in modo da incastrarsi con precisione con i denti di un'altra ruota dentata o con una catena, una cinghia o un pignone.
Le ruote dentate sono caratterizzate da diverse proprietà, tra cui il numero di denti, il modulo (la dimensione dei denti), il diametro primitivo (il diametro teorico in cui i denti si incastrano perfettamente con quelli di un'altra ruota dentata), il passo (la distanza tra i centri di due denti consecutivi) e il profilo dei denti.
La corretta scelta delle ruote dentate, in termini di dimensioni e rapporti di trasmissione, è fondamentale per garantire un funzionamento efficiente e affidabile del sistema meccanico in cui vengono utilizzate.
Camma ed eccentrico[modifica | modifica wikitesto]

una camma è un elemento meccanico che viene utilizzato per trasformare un moto rotatorio in un moto alternativo o viceversa. Consiste in genere in un disco o un cilindro con una superficie profilata chiamata profilo della camma.
La forma del profilo della camma determina il movimento del cosiddetto "seguito di camma", che può essere una leva, una linguetta, un pistone o un'altra parte meccanica. Quando la camma ruota, il profilo della camma fa sì che il seguito di camma si sposti in un determinato modo. Questo movimento può essere un'alternanza tra movimento lineare e fermo, un movimento oscillante o un movimento complesso e personalizzato.

L'eccentrico è montato sull'albero motore o su un albero rotante e, durante la rotazione, genera un movimento non uniforme o un'oscillazione nel seguito di eccentrico, che può essere una leva, una linguetta o un'altra parte meccanica. A differenza di una camma, l'eccentrico produce un movimento uniforme lungo una linea retta anziché un profilo curvilineo.
Trasmissione a cinghia o a catena[modifica | modifica wikitesto]
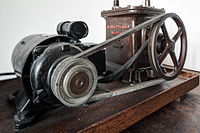
Una trasmissione a cinghia è un tipo di meccanismo utilizzato per trasferire il movimento e la potenza tra due alberi rotanti che non sono fisicamente collegati. Questa trasmissione avviene attraverso una cinghia, una banda flessibile solitamente realizzata in materiale elastico come la gomma, che scorre sui pulegge, detti anche ingranaggi a cinghia o pignoni, poste sugli alberi. Le trasmissioni a cinghia offrono diversi vantaggi rispetto ad altri metodi di trasmissione, come le trasmissioni ad ingranaggi o a catena. Tra i vantaggi principali troviamo l'assorbimento degli urti, la riduzione del rumore, la riduzione dell'usura e la facilità di installazione e manutenzione.
La trasmissione a catena è identica nelle funzionalità ma si utilizza al posto della cinghia una serie di maglie interconnesse, solitamente realizzate in metallo, che scorrono su pignoni o ruote dentate. Le catene di trasmissione offrono numerosi vantaggi, tra cui la resistenza, trasmissione efficiente della potenza, precisione di lavoro, lunga durata e adattabilità agli ambienti d'uso.
Biella e manovella[modifica | modifica wikitesto]
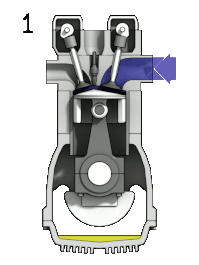
Il meccanismo biella-manovella permette di convertire il movimento rotatorio in movimento lineare (e viceversa). È composto da due componenti principali: la biella e la manovella. La manovella è un'asta rigida collegata a un albero rotante. La biella è un'asta che collega la manovella a un punto di attacco mobile, come un pistone o un'altra parte che deve muoversi linearmente. La manovella ruota attorno al suo asse e il movimento rotatorio viene convertito in movimento lineare della biella.
Il funzionamento del meccanismo biella-manovella si basa sul fatto che la distanza tra l'asse di rotazione della manovella e l'asse della biella è costante. Quando la manovella ruota, la biella si muove in su e in giù (o avanti e indietro) in un movimento lineare. Il punto di attacco della biella può essere progettato per svolgere varie funzioni, come ad esempio convertire il movimento lineare in rotazione o viceversa.
La progettazione e l'ottimizzazione del meccanismo biella-manovella richiedono un'attenta considerazione dei parametri come la lunghezza della biella, l'angolo di rotazione della manovella e la forza applicata sulla biella. Questi fattori influenzano l'escursione lineare, la velocità e la coppia del sistema.
Attuatori idraulici[modifica | modifica wikitesto]

Gli attuatori idraulici utilizzano un fluido incompressibile, solitamente olio idraulico, per generare una forza e un movimento. Questi attuatori sono costituiti da un cilindro idraulico, un pistone e un sistema di valvole. Quando il fluido viene pompato nel cilindro, spinge il pistone in una direzione, generando un movimento lineare o rotativo. Gli attuatori idraulici sono noti per la loro capacità di generare forze elevate e vengono spesso utilizzati in applicazioni che richiedono una potenza significativa, come gru, presse e macchinari pesanti.
I fluidi idraulici utilizzati possono essere oli idraulici (fluidi incompressibili) o gas compressi, come l'aria (fluidi compressibili). L'olio idraulico viene spesso preferito per le applicazioni che richiedono elevate forze o precisione di controllo, mentre l'aria compressa viene utilizzata in sistemi pneumatici che richiedono velocità o movimenti leggeri.
I sistemi idraulici sono costituiti da componenti chiave, tra cui pompe, valvole, attuatori (come cilindri o motori idraulici) e tubi flessibili o rigidi per il trasferimento del fluido. Le pompe creano pressione nel fluido, che viene poi regolato e controllato dalle valvole. L'energia idraulica viene quindi convertita in movimento o forza attraverso gli attuatori. In sintesi, l'idraulica in meccanica si riferisce all'utilizzo dei fluidi (incompressibili o compressibili) per il controllo e il movimento dei componenti meccanici, consentendo la trasmissione di forza e l'esecuzione di operazioni precise e potenti.
Attuatori pneumatici[modifica | modifica wikitesto]

Gli attuatori pneumatici utilizzano aria compressa per generare una forza e un movimento. Sono costituiti da un cilindro pneumatico, un pistone e un sistema di valvole. Quando l'aria compressa viene fornita al cilindro, spinge il pistone, generando un movimento lineare. Gli attuatori pneumatici sono ampiamente utilizzati in molte industrie, grazie alla loro semplicità, velocità di risposta rapida e facilità di controllo. Sono spesso utilizzati in applicazioni di automazione industriale, come robotica, macchinari di assemblaggio e attuatori per porte.
Questi attuatori vengono solitamente utilizzati per eseguire operazioni di spinta, trazione, sollevamento, rotazione e altro ancora. L'aria compressa viene generata da compressori pneumatici e viene distribuita attraverso tubi e valvole pneumatiche per raggiungere gli attuatori. Le valvole pneumatiche controllano il flusso dell'aria e permettono di regolare la direzione, la velocità e la forza del movimento degli attuatori.
Attuatori elettromeccanici[modifica | modifica wikitesto]

Gli attuatori elettromeccanici convertono l'energia elettrica in un movimento meccanico. Questi attuatori utilizzano un motore elettrico, come un motore a corrente continua (DC) o un motore passo-passo, per generare un movimento rotativo o lineare.
Nel contesto della trasmissione elettrica del moto, il motore elettrico è collegato meccanicamente a un sistema di trasmissione, come ad esempio un albero di trasmissione, pulegge, ingranaggi o cinghie, che permette di trasferire il movimento generato dal motore alle parti meccaniche che si desidera far funzionare. La trasmissione elettrica del moto offre diversi vantaggi, come l'alta efficienza energetica, la regolabilità della velocità e la facilità di controllo. Inoltre, i motori elettrici possono essere alimentati da diverse fonti di energia, inclusi sistemi di alimentazione a batteria o tramite reti elettriche.
Standard internazionali[modifica | modifica wikitesto]
Le normative in meccanica servono a garantire la qualità, la sicurezza, l'interoperabilità e l'affidabilità dei prodotti e dei servizi nel campo della progettazione e produzione meccanica. Svolgono un ruolo fondamentale per l'industria, fornendo linee guida, specifiche e requisiti che gli operatori devono seguire.
- ISO (Organizzazione internazionale per la normazione): L'ISO sviluppa una vasta gamma di standard tecnici che coprono diversi aspetti della progettazione, produzione e gestione nella meccanica e in altri settori. Gli standard ISO sono ampiamente accettati a livello internazionale e forniscono linee guida per garantire la qualità, la sicurezza e l'efficienza dei prodotti e dei servizi.
ASME (American Society of Mechanical Engineers): L'ASME sviluppa standard nel campo dell'ingegneria meccanica, con particolare attenzione alla progettazione, alla fabbricazione e all'ispezione di apparecchiature e componenti meccanici. I loro standard sono utilizzati negli Stati Uniti e in molti altri paesi come riferimento per l'industria.
ASTM International (American Society for Testing and Materials): ASTM International sviluppa standard tecnici che coprono una vasta gamma di settori, tra cui la meccanica. I loro standard definiscono le specifiche dei materiali, le procedure di test e le linee guida per garantire la qualità e la sicurezza dei prodotti meccanici.
DIN (Deutsches Institut für Normung): DIN è l'organizzazione tedesca per la normazione e sviluppa standard utilizzati principalmente in Germania. I loro standard coprono diverse aree della meccanica e definiscono specifiche tecniche, procedure di test e altre linee guida.
BS (British Standards): Il BSI Group sviluppa standard tecnici nel Regno Unito, compresi quelli relativi alla meccanica. I loro standard definiscono specifiche tecniche, procedure di test e linee guida per garantire la qualità e la sicurezza dei prodotti meccanici nel contesto britannico.
ANSI (American National Standards Institute): L'ANSI coordina lo sviluppo e la promozione degli standard nazionali negli Stati Uniti. L'ANSI adotta standard in diversi settori, inclusa la meccanica, che sono riconosciuti a livello nazionale e internazionale per garantire l'efficienza, la sicurezza e la qualità dei prodotti meccanici.
L'UNI (Ente Nazionale Italiano di Unificazione) è l'organizzazione italiana per la normazione tecnica. L'UNI sviluppa e promuove gli standard tecnici in diversi settori, compresa la meccanica, in Italia. I suoi standard sono ampiamente utilizzati e accettati nel paese come riferimento per la progettazione, la produzione e la valutazione dei prodotti meccanici.
Note[modifica | modifica wikitesto]
Bibliografia[modifica | modifica wikitesto]
- Luigi Calligaris, Stefano Fava e Carlo Tomasello, Manuale di meccanica, Hoepli, 2016, ISBN 978-88-203-6645-2.
- Luigi Baldassini e Lorenzo Fiorinesci, Vademecum per disegnatori e tecnici, 2022 [1955], ISBN 978-88-360-0010-4.